LEWCO Drum Heating Tunnels provide a means to heat individual drums that are not palletized, while also accommodating “first-in, first-out” product flow. These models also offer the potential for automated drum handling and integration into other processes. This model features integrated spill containment and is suitable for indoor use only. All models feature our signature all-welded steel, heavy-duty construction and simple, user-friendly controls. Each unit comes complete with a (3) year warranty and is fully assembled, wired, and tested prior to shipment.
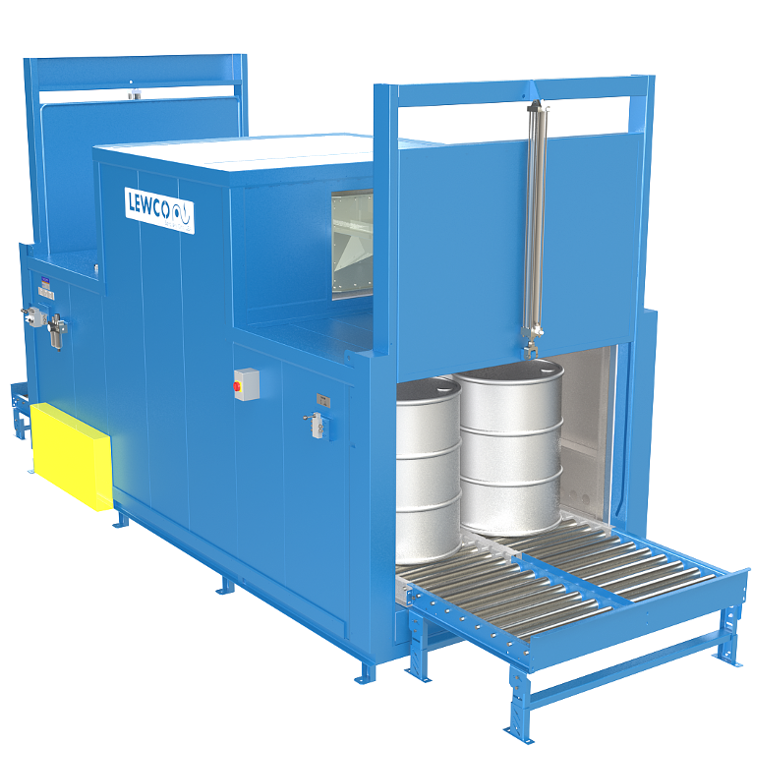
Operating Temperature
125°F (52°C) to 175°F (79°C)
Capacity
(16) 55-gallon drums; 675 lbs. per drum
Heat Source & Capacity
Saturated steam, 10-200 PSIG . All heat exchangers are welded by A.S.M.E. certified welders and then hydro-tested at 300 PSIG.
- Heat Exchanger: 124,000 BTU’s per hour @ 150 PSIG
- Hot oil and hot water (5-100 PSIG) also available.
Circulation Fan
3,500 CFM, TEFC motor. Explosion-proof motor also available.
Input Voltage
Standard: 480/3/60. Please consult factory for additional voltage options.
Additional Options
- 5″ exhaust vent with damper
- Steam trap, 0-29 PSIG
- Stainless steel construction
Control System Options
- No controls
- Non-electronic, self-acting temperature controller, limited to 150 psig, available in the following ranges:
- 125°-212°F, ½” valve
- 158°-300°F, ½” valve
- Single set-point digital temperature controller and redundant high-limit controller housed in a NEMA 12 enclosure with full voltage lockable disconnect switch. Controls are designed and wired to NFPA 70 and 79 electrical standards in our own UL508A certified panel shop. Independent third party inspections available.
Electronic Control Options:
-
- NEMA 7 explosion-proof enclosure
-
- IP65 enclosure (meets NEMA 12, 3R, and 4X)
-
- Batch Timer: Infinitely adjustable up to 100 hours; includes illuminated On/ Off switch to indicate timed operation and audible alarm when time has elapsed.
-
- Chart Recorder: Single pen circular paper chart recorder for continuous monitoring of temperature data. Comes with (1) Type “J” thermocouple input.
-
- Data Logger: Multiple input digital data logger continuously records temperature and other process data. Allows downloading of digital data files through USB or Ethernet connection. Data can also be viewed on a full color display or on a web server when connected to a network.
-
- Door Switch: Automatically disables heat when door is opened.
-
- Ramp/ Soak Controller: Programmable ramp/ soak temperature controller with capability to store different recipes with multiple segments.
Standard construction includes an all welded 1/8″ steel shell with 3″ x 6# mineral wool insulation. Heat loss is minimized by a proprietary wall design featuring a welded inner shell and a completely isolated outer frame and covers. A top mounted heater box saves floor space and provides high-convection airflow for faster heat-up times. This model features top-mounted lifting eyes for easy installation and transportation.
Conveyor
- Gravity roller conveyor set on incline to efficiently convey drums through tunnel.
- 2 ½” diameter x 11 gauge rollers with sealed bearings on 4 ½” roller centers.
- Proprietary escapement device allows discharge of (1) drum at a time.
- A variety of powered and unpowered standard conveyor options and configurations are available.
Spill Containment
- 111 gallon capacity
- Sump drain, 1” NPT
Doors
- Pneumatic vertical lift guillotine doors on both ends provides convenient drum entry and exit
- Requires compressed air at 60 PSI
Finish
- Standard: Blue or gray alkyd enamel
- Optional: Premium finish for corrosive environments
- Viscosity Reduction
- Melting
- Continuous Process
LEWCO Drum Heating Tunnels are designed and manufactured to industry standards. Our engineers stay current with the latest revisions to these standards. If there is a specific industry standard or code compliance that you require for your process heating application, please contact one of our highly knowledgeable Applications Engineers to learn how LEWCO can help!
Industry Standards