LEWCO Enhanced Duty Batch Ovens offer all of the same construction features as the normal duty ovens; however the performance is “enhanced” by adding additional heat capacity and larger circulation fans. Additionally, all enhanced duty walk-in ovens guarantee a temperature uniformity of +/- 10°F. The EWR series features a rear-mounted heater box, which is ideal for installations with height restrictions. Each unit comes complete with a one-year warranty and is fully assembled, wired, and tested prior to shipment. All LEWCO ovens are manufactured to meet the requirements of NFPA 86, the national standard for ovens and furnaces.
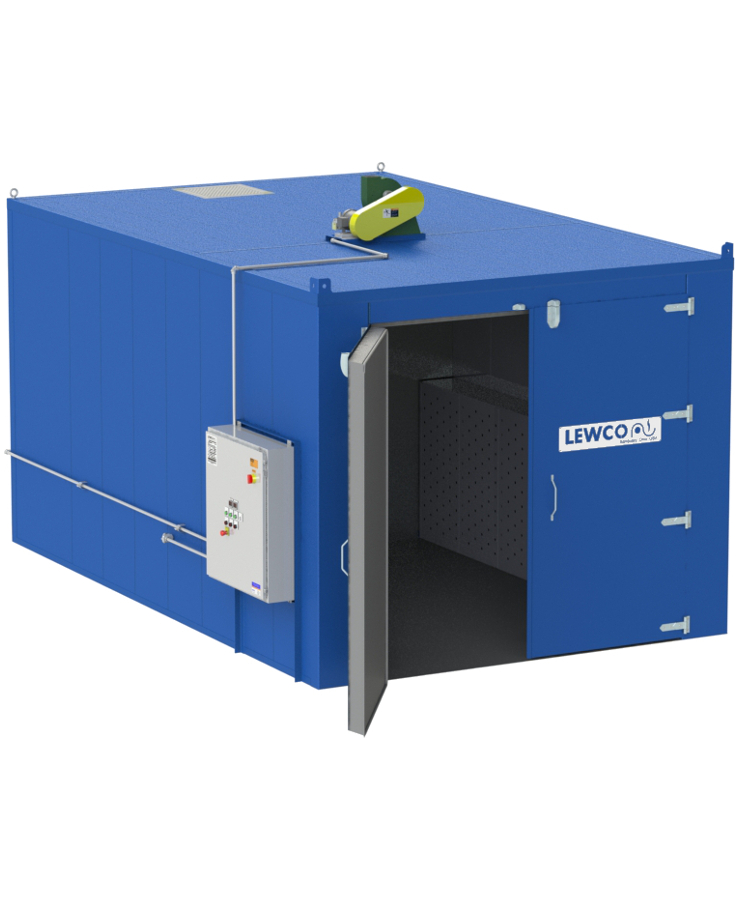
Operating Temperature
200°F (93°C) to 1200°F (649°C)
Heating Medium
Direct fired natural gas modulating burner with direct coupled, digital actuated control valve. High turndown ratio allows for rapid heat-up and tight temperature controls.
- Low CO and NOX emissions
- F.M. compliant fuel train
Airflow Pattern
Dual (Combination) Airflow: Hot air is supplied from both of the side walls and returned through a top plenum.
Input Voltage
Standard: 480/3/60. Please consult factory for additional options.
Control System
LEWCO’s standard control package includes a single set-point process temperature controller and redundant high-limit controller. Circulation fan(s) and exhaust fan(s) include air proving circuits that are electrically interlocked with the heating circuit. All controls are housed in a NEMA 12 enclosure employing a full voltage lockable disconnect switch. Ovens operating at or above 800°F include a zero speed switch for fans. Controls are wired to NFPA 70 and 79 electrical standards in our own UL508A certified panel shop. Independent third party inspections available.
Model (NFPA Class B) | Overall Dimensions | Door Swing Radius | Workspace Dimensions | Burner (BTU/ Hr) | Circulating Fan (CFM) |
Motor (HP) |
Air Changes per Minute | Exhaust Fan Capacity (CFM) | Exhaust Motor (HP) | Solvents per Batch (Gals.) |
Ships Fully Assembled | ||||
“W | “D | “H | “W | “D | “H | ||||||||||
EWR12FD-48-48-60
|
94 | 118 | 117 | 24″ | 48 | 48 | 60 | 400,000 | 3,500 | 3 | 43.75 | 500 | 1 | 0 | Yes |
EWR12FD-48-48-72
|
94 | 124 | 129 | 24″ | 48 | 48 | 72 | 400,000 | 4,000 | 3 | 41.67 | 500 | 1 | 0 | Yes |
EWR12FD-48-48-96
|
98 | 128 | 153 | 24″ | 48 | 48 | 96 | 400,000 | 5,000 | 3 | 39.06 | 500 | 1 | 0 | No |
EWR12FD-48-72-72
|
98 | 158 | 129 | 24″ | 48 | 72 | 72 | 400,000 | 5,500 | 3 | 38.19 | 500 | 1 | 0 | Yes |
EWR12FD-48-72-96
|
106 | 158 | 153 | 24″ | 48 | 72 | 96 | 700,000 | 8,000 | 5 | 41.67 | 750 | 1 | 0 | No |
EWR12FD-48-96-72 | 106 | 182 | 129 | 24″ | 48 | 96 | 72 | 700,000 | 8,000 | 5 | 41.67 | 750 | 1 | 0 | Yes |
EWR12FD-48-96-96 | 110 | 189 | 153 | 24″ | 48 | 96 | 96 | 700,000 | 10,000 | 7 1/2 | 39.06 | 750 | 1 | 0 | No |
EWR12FD-60-60-60
|
110 | 140 | 117 | 30″ | 60 | 60 | 60 | 400,000 | 5,000 | 3 | 40.00 | 500 | 1 | 0 | Yes |
EWR12FD-60-60-72 | 112 | 146 | 129 | 30″ | 60 | 60 | 72 | 400,000 | 6,000 | 3 | 40.00 | 500 | 1 | 0 | Yes |
EWR12FD-60-60-96 | 118 | 146 | 153 | 30″ | 60 | 60 | 96 | 700,000 | 8,000 | 5 | 40.00 | 750 | 1 | 0 | No |
EWR12FD-60-72-72 | 114 | 158 | 129 | 30″ | 60 | 72 | 72 | 400,000 | 7,000 | 5 | 38.89 | 500 | 1 | 0 | Yes |
EWR12FD-60-72-96 | 122 | 165 | 153 | 30″ | 60 | 72 | 96 | 700,000 | 10,000 | 7 1/2 | 41.67 | 750 | 1 | 0 | No |
EWR12FD-60-96-96 | 132 | 194 | 153 | 30″ | 60 | 96 | 96 | 700,000 | 14,000 | 10 | 43.75 | 750 | 1 | 0 | No |
EWR12FD-72-72-72
|
134 | 158 | 129 | 36″ | 72 | 72 | 72 | 700,000 | 9,000 | 7 1/2 | 41.67 | 750 | 1 | 0 | Yes |
EWR12FD-72-72-96 | 138 | 170 | 153 | 36″ | 72 | 72 | 96 | 700,000 | 12,000 | 7 1/2 | 41.67 | 750 | 1 | 0 | No |
EWR12FD-72-96-96 | 146 | 203 | 153 | 36″ | 72 | 96 | 96 | 700,000 | 16,000 | 10 | 41.67 | 750 | 1 | 0 | No |
Note: Sizes are approximate. LEWCO, Inc. reserves the right to change specifications without notice.
Standard oven construction includes a 16 gauge stainless steel interior with a 3/16″ plate steel exterior. Heat loss is minimized by a unique wall design featuring a welded inner shell and a completely isolated outer frame and covers.
Doors
Heavy-duty vertical lift, guillotine style door on an isolated door frame minimizes heat loss. Wire core gaskets create a tight seal for efficient heating.
Flooring
Standard ovens operating at or above 650°F include an insulated base (100 p.s.f. max)
Standard Options:
- Insulated with (1) pair inverted angle track
- Insulated with (1) pair 6” wide wheel guides
- Aging Ovens: Used to accelerate the aging process of materials like plastics, rubber, or aluminum to test their long-term durability and performance. They can also be used for heat treatment to increase the strength of aluminum parts.
- Annealing Ovens: Function by heating materials above their recrystallization temperature (but below their melting temperature) to form new grains without residual stress, improving ductility and relieving internal stresses.
- Composite Curing Ovens: Used to cure, anneal, dry, and/or harden composite materials. These are often found in aerospace, automotive, and military industries.
- Drying Ovens: Heated chambers specifically designed to remove moisture or water from various materials. They are used in labs and industrial settings for tasks like drying samples, sterilizing equipment, and preparing products for further processing.
- Finishing Ovens: Used in manufacturing processes to apply coatings (like wet paint or powder coating) to products, which protects them from corrosion and wear.
- Heat Treating Ovens: General term for ovens used to alter the physical and chemical properties of materials, usually metals, through controlled heating and cooling.
- Industrial Curing Ovens: Ovens used to solidify epoxies or plastics, or to cure coatings and adhesives on surfaces, leading to chemical reactions that finish or harden products.
- Normalizing Ovens: Similar to annealing, they involve heating a material above its recrystallization temperature (but below its melting temperature) followed by air cooling to refine the grain structure, improve mechanical properties, and relieve internal stresses.
- Paint Baking Ovens: Specifically designed to heat paint to facilitate the curing reaction, creating a stronger bond between the paint and surface.
- Preheating Ovens: Used to prepare materials for subsequent processes, such as heating products before coating or welding.
- Stress Relieving Ovens: Used to heat and cool metals at specific rates and temperatures to relieve internal stresses developed during manufacturing processes, enhancing resistance to cracking, deformation, and wear.
LEWCO industrial ovens are designed and manufactured to industry standards. Our engineers regularly work to keep updated with the latest revisions in industry codes. If there is a specific industry standard or code compliance that you require for your process heating application, please contact one of our highly knowledgeable applications engineers to learn how LEWCO can help!
About NFPA 86
The National Fire Protection Association’s standard, NFPA 86, documents the guidelines for the safe operation of industrial ovens and furnaces. All LEWCO ovens are designed and manufactured to meet the requirements of this standard. Oven and furnaces in which flammable volatiles or combustible materials are present in the work space are classified by NFPA 86 as “Class A.” Similarly, ovens and furnaces in which no flammable volatiles or combustible materials are present are classified as “Class B.” Due to the risk of fire or explosion, NFPA 86 requires specific safety equipment for all Class A ovens and furnaces. Fuel gas-fired ovens and furnaces also require safety equipment.
- Powered exhaust of capacity determined by maximum solvent loading.
- Explosion relief of adequate area determined by oven or furnace workspace volume.
Industry Standards